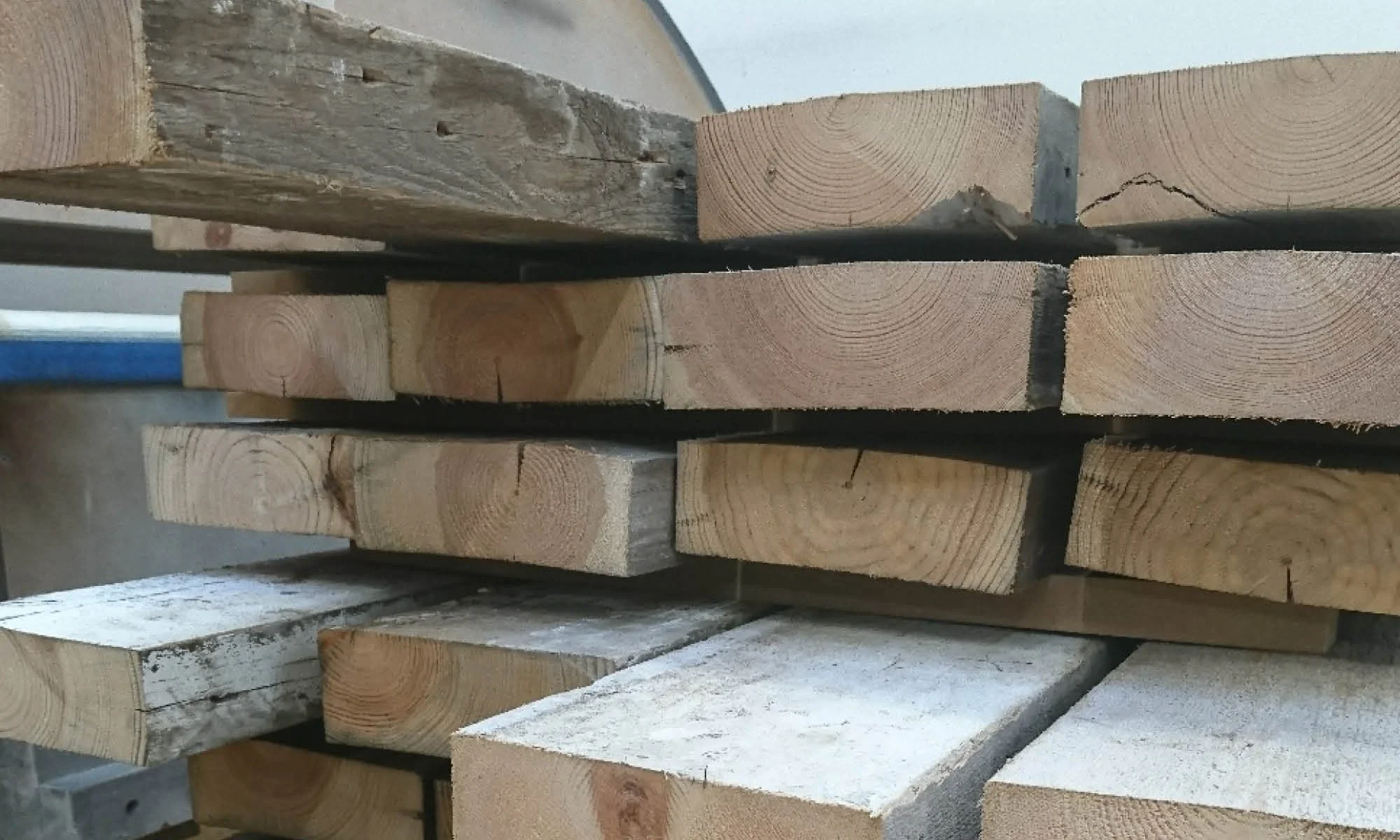
Our commitment
to sustainability
We take environmental sustainability as seriously as we take furniture design. Our pieces are durable and timeless by design resulting in greater longevity in service. Opus Magnum has ISO14001 certification, and this commits us to a monitored programme of continuous environmental improvement.
From conscious material sourcing to using water-based finishing lacquers, every stage of our furniture design and manufacturing process is carefully considered against its environmental impact.
From the beginning
Whenever possible our wood is sustainable. Opus Magnum has Forest Stewardship Council® (FSC®) certification. All products are available as FSC certified upon request at the point of order. That means ensuring every stage — from forest to final delivery — can be traced and accounted for to ensure that it is produced in a sustainable way.
We also reuse or recycle whatever we can to reduce waste. For example, our FSC certification allows us to collect post-consumer reclaimed wood and incorporate this material into new products.
Good energy
The fully automatic biomass boiler in our workshop uses sawdust and timber waste for our spray booth and workshop heating. Our boiler emissions are processed and cleaned according to strict environmental regulations.
Solar panels have been installed on the factory roof space. These now produce approximately a third of our total annual electricity requirement.
We’ve also found multiple ways to reduce our energy consumption including changing our lighting to LED, cycle to work scheme and investment in new equipment like the latest air compressor.
Designs that last
Our life furniture is designed and built to last. How? Components are dry-jointed rather than glued, so individual parts can be replaced if damaged, or redressed with different materials to better suit your new space.
Masters of ReCrafting
We’re not just good at making furniture, we’re good at remaking it too. We call it ReCrafting, because the work we do goes way beyond restoring and refinishing.
When ReCrafting, we give unhappy commercial furniture a new lease of life — whether that’s offering salvaged softwood ceiling joists a new career as elegant dining tables, or cutting back and retrofitting old meeting tables to meet the needs of today’s (and tomorrow’s) tech.
Boosting the circular economy
By breathing new life into existing and unwanted pieces of furniture, we’re contributing to the circular economy. That means less strain on natural resources, less perfectly good raw materials going to landfill, and less energy wasted in the process.
Cutting the carbon
With every piece of brand-new furniture you add to your space, the carbon emissions keep racking up. Our recrafting projects are different. We take part of the post-consumer waste from commercial buildings to create new bespoke pieces that meet the needs of the new interior — avoiding those carbon emissions tallying up in the process.
Our recrafting process also relies on our close proximity to our market. In other words, our furniture doesn’t travel very far.
Whittling down waste
The extraction, manufacturing, and transport of raw materials leads to more Scope 3 emissions. By avoiding new raw materials, we’re avoiding this eco-unfriendly chain — and all the wasted energy and materials that go with it. And we always strive to use as much of the raw material that arrives at our Wandsworth workshop as we can in every single piece.
ReCrafting in action
-
ReCrafting for Mediabrands
A visit to site uncovered various old and worn items that could be salvaged. We used our local workshop, skills and creativity to manufacture new coffee table tops from the post-consumer reclaimed timber.
-
ReCrafting old ceiling joists
What to do with a stack of softwood ceiling joists from the Department Store in Brixton that dated back to 1906?
After much experimentation the material was converted into a series of end grain blocks and long grain hand cut veneers. This beautiful ‘new’ material was then used to create two large meeting and dining tables. The carbon stored safely for another generation.
-
ReCrafting for Baird Capital
The team collected several worn, walnut tabletops and leg frames that were no longer suitable for their business needs. These were returned to the workshop for ReCrafting – a journey distance of 6 miles.
We then re-sized the tops to suit the new office layout, added cable management flaps and removed the damaged walnut layer so that it could be replaced with new European oak veneer. This process reused the 40mm thick substrate material and all the steel leg frames.